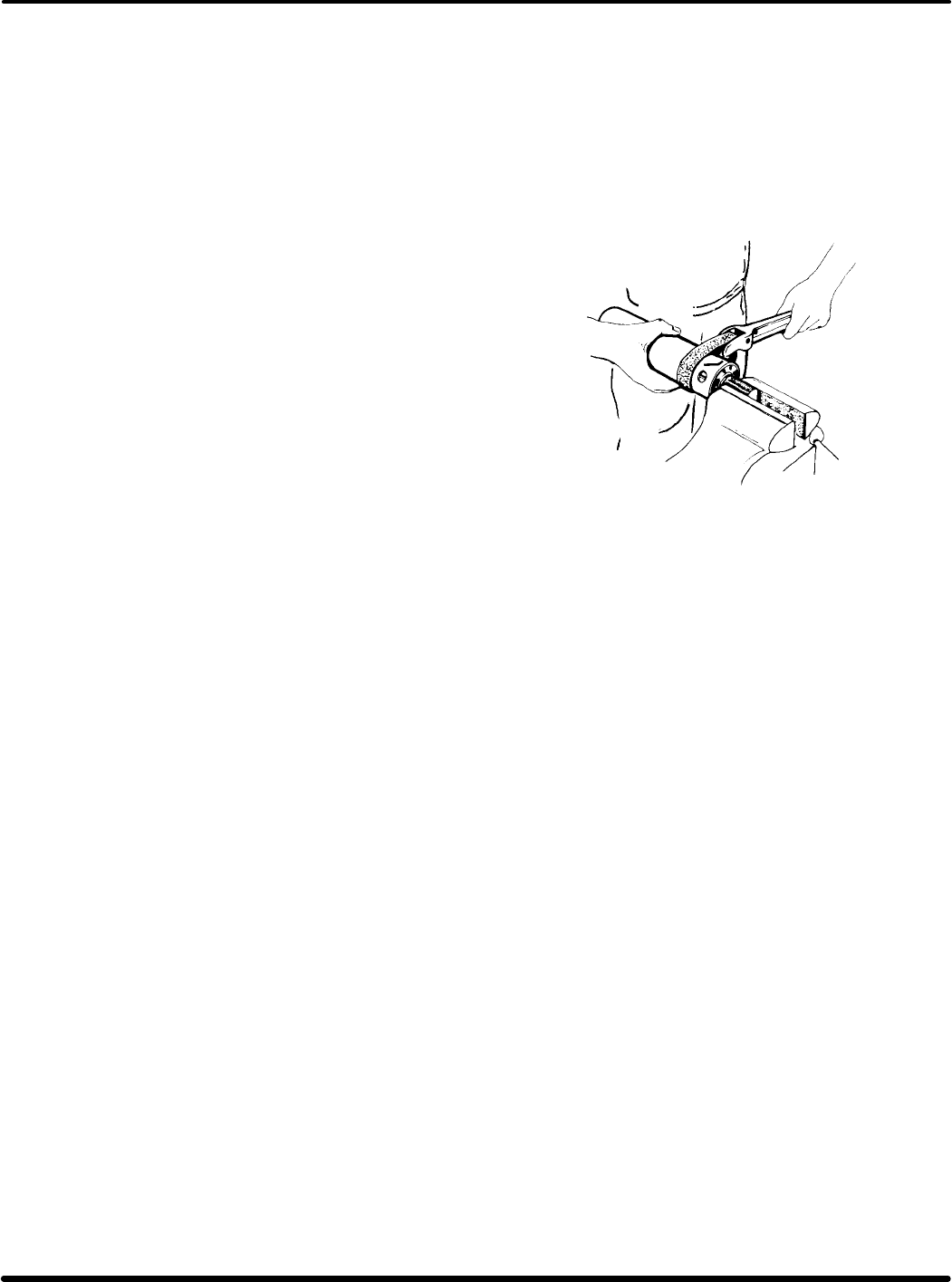
Economair Cylinders2OF8
Warnings
and Service Information
WARNINGS:
Improper application, installation, service or maintenance of
AROR
cylinders may create a hazardous condition,
which may in
turn
cause bodily injury
as well as shortened product life. Contact
The
Aro Corporation for special applications.
ECONOMAIR
CYLINDER APPLICA
TION
S Economair
cylinders are a series of round line repairable
cylinders designed for medium to heavy duty pneumatic
applications.
S
The operating pressures are 200 p.s.i.g. - pneumatic and
200 p.s.i.g. - non-shock hydraulic with hydraulic packing
option.
S
Economair cylinders are available in 6 bore sizes: 1-1/8”,
1-1/2”, 2”, 2-1/2”, 3” and 4”.
S
Options include : 6 mounting styles, magnetic pistons,
cushioned and non-cushioned and numerous packing op-
tions.
CUSHIONS
24 and 28 series cylinders
are cushioned models. Cushions are
protective devices used to extend cylinder life and should not be
used to decelerate loads.
Cushioning on all bores, except the 1-1/8”, are equiped with an
adjustable needle valve in the head and cap to provide adjust-
ment
of the cushion ef
fect - clockwise rotation increases cushion
-
ing, counterclockwise rotation decreases cushioning. After ad-
justment,
tighten retaining nut to
lock into position. CAUTION: Do
not
disengage cushion needle from head or cap
while cylinder is
under
pressure.
OPERATION
AND MAINTENANCE
Pneumatic cylinders should be lubricated to provide maximum
cycle life. Economair cylinders are lubricated with Shell
Darina,
EP
grade, no. 2 grease during assembly at our factory in Angola,
Indiana.
Factory lubrication will provide a satisfactory amount of
cycle
life if no additional lubrication is provided.
However
, we rec
-
ommend
lubrication for any pneumatic system and suggest that
you
follow the guidelines for types of lubricants
which are outlined
in
all of our catalogs (reference catalog 0020-M).
Periodic maintenance must be performed to assure maximum
product
life. Disassembly for cleaning, inspection, and relubrica
-
tion
can be performed any time equipment is idle for a short period
of
time.
All metal parts should be cleaned with a non-flammable
solvent.
All rubber parts should be thoroughly washed with soap
and water. Cleaned parts should be rinsed and dried with low
pressure
air
. Any parts which are worn or damaged should be re
-
placed.
Selected parts and seals are available in repair kit form.
DISASSEMBLY
Clamp
head by nose or tang flats with port in a vertical position at
top
of cylinder
.
Remove all fittings, rotate barrel counterclockwise with a strap
wrench
one
full turn. Locking wire will feed out of slot during turn
-
ing.
At the completion of revolution, remove retaining wire, wiggle
barrel
and slide from head.
ASSEMBLY
Verify
that all
seals are in the correct position and that the rod and
piston
seals have been properly lubricated with Shell Darina, Ep
grade no. 2 grease or equivalent.
Slide
piston rod in head (be sure not to damage “U” cup in head),
then slide barrel over piston onto head. Avoid damaging piston
seals
or head
“O” ring. Clamp head by nose or tang on flats with
port in a vertical position.
Align port and hole in barrel; insert retaining wire tap in hole in
head
in feed slot. Rotate barrel
with strap wrench clockwise one
revolution,
until port and hole align; retaining wire will feed as bar
-
rel
turns.
The assembled cylinder can now be tested for
leaks and proper
operation.
1. Alternately
apply 90 p.s.i.g. air pressure to each of the cylinder
ports and test for internal leaks across
the
piston and external
leaks
at the barrel seals and the rod seals.
2. T
est for proper cycling at 20 p.s.i.g. supply
.