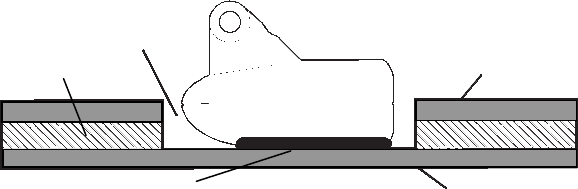
19
If the arch slopes up – but not back down – then the front of the trans-
ducer is too high and needs to be lowered. If only the back half of the
arch is printed, then the nose of the transducer is angled too far down
and needs to be raised.
NOTE:
Periodically wash the transducer's face with soap and water to re-
move any oil film. Oil and dirt on the face will reduce the sensitivity
or may even prevent operation.
SHOOT-THRU-HULL PREPARATION
The transducer installation inside a fiberglass hull must be in an area
that does not have air bubbles in the resin or separated fiberglass lay-
ers. The sonar signal must pass through solid fiberglass. A successful
transducer installation can be made on hulls with flotation materials
(such as plywood, balsa wood or foam) between layers of fiberglass if
the material is removed from the chosen area.
Epoxy the transducer to a solid portion of the hull.
For example, some (but not all) manufacturers use a layer of fiberglass,
then a core of balsa wood, finishing with an outer layer of fiberglass.
Removing the inner layer of fiberglass and the balsa wood core exposes
the outer layer of fiberglass. The transducer can then be epoxied di-
rectly to the outer layer of fiberglass. After the epoxy cures, the hull is
watertight and structurally sound. Remember, the sonar signal must
pass through solid fiberglass. Any air bubbles in the fiberglass or the
epoxy will reduce or eliminate the sonar signals.
Fill with epoxy
Inner hull
Epoxy to hull first
Outer hull
Flotation material