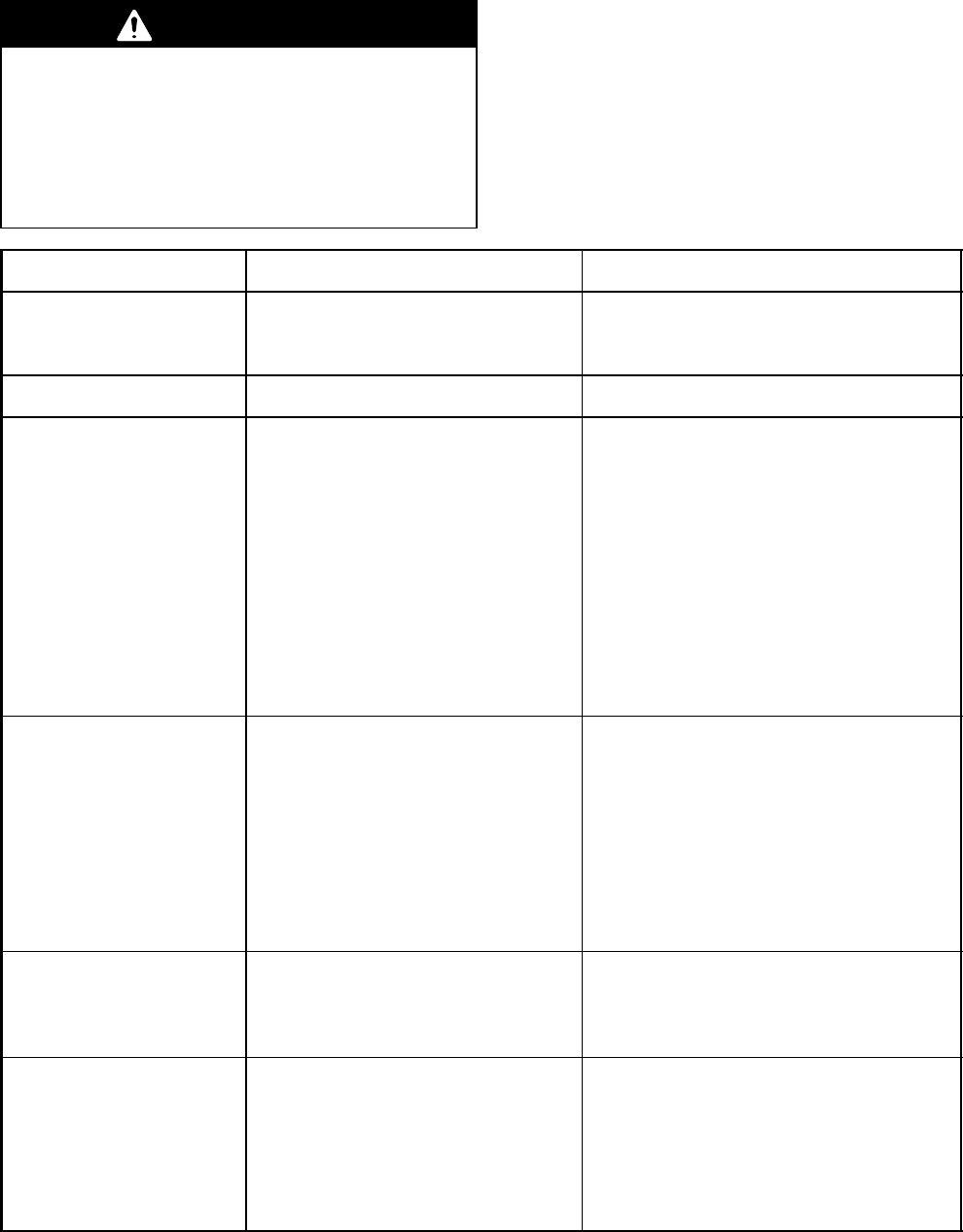
10 308647
Troubleshooting
WARNING
To reduce the risk of serious bodily injury, including
skin injection, splashing in the eyes or on the skin,
or injury from moving parts, always follow the Pres-
sure Relief Procedure on page 5 whenever the
pump is shut off, before installing, cleaning, adjust-
ing, removing, or servicing the valve or any part of
the system, and whenever you stop dispensing.
NOTE: Check all possible solutions in the chart below
before you disassemble the regulator.
Problem
Cause Solution
No pressure regulation Damaged diaphragm Replace diaphragm.
Leaking or dirty seat Replace cartridge, or clean seat.
No fluid flow Damaged valve actuator Replace valve actuator.
Pressure creeps above
setting
Metal chip or contamination
between ball and seat
Replace cartridge, or clean seat area.
Damaged diaphragm Replace diaphragm.
Damaged o-ring or improper seal Replace the o-ring under the seat.
Damaged or clogged air regulator or
line (air-operated regulator only)
Clear obstruction in line. Service regula-
tor if necessary.
Leaking or dirty seat Replace cartridge, or clean seat.
Large change in inlet pressure Stabilize regulator inlet pressure.
Pressure drops below
setting
Empty/clogged supply line Fill/flush supply line.
Damaged or clogged air regulator or
line (air-operated regulator only)
Clear obstruction in line. Service regula-
tor if necessary.
Using valve beyond its rated flow
capacity
Install valve for each spray gun or
dispensing valve.
Large change in inlet pressure Stabilize regulator inlet pressure.
Fluid leaks from spring
housing
Loose fluid housing Tighten the four cap screws.
Damaged diaphragm Replace diaphragm.
Chatter Excessive pressure differential
between pump and gun
Reduce pump pressure to not more than
2000 psi (14 MPa, 138 bar) greater than
required gun pressure.
Excessive flow rate Reduce fluid flow through regulator.
Connect only one spray gun or dispens-
ing valve to each fluid regulator.