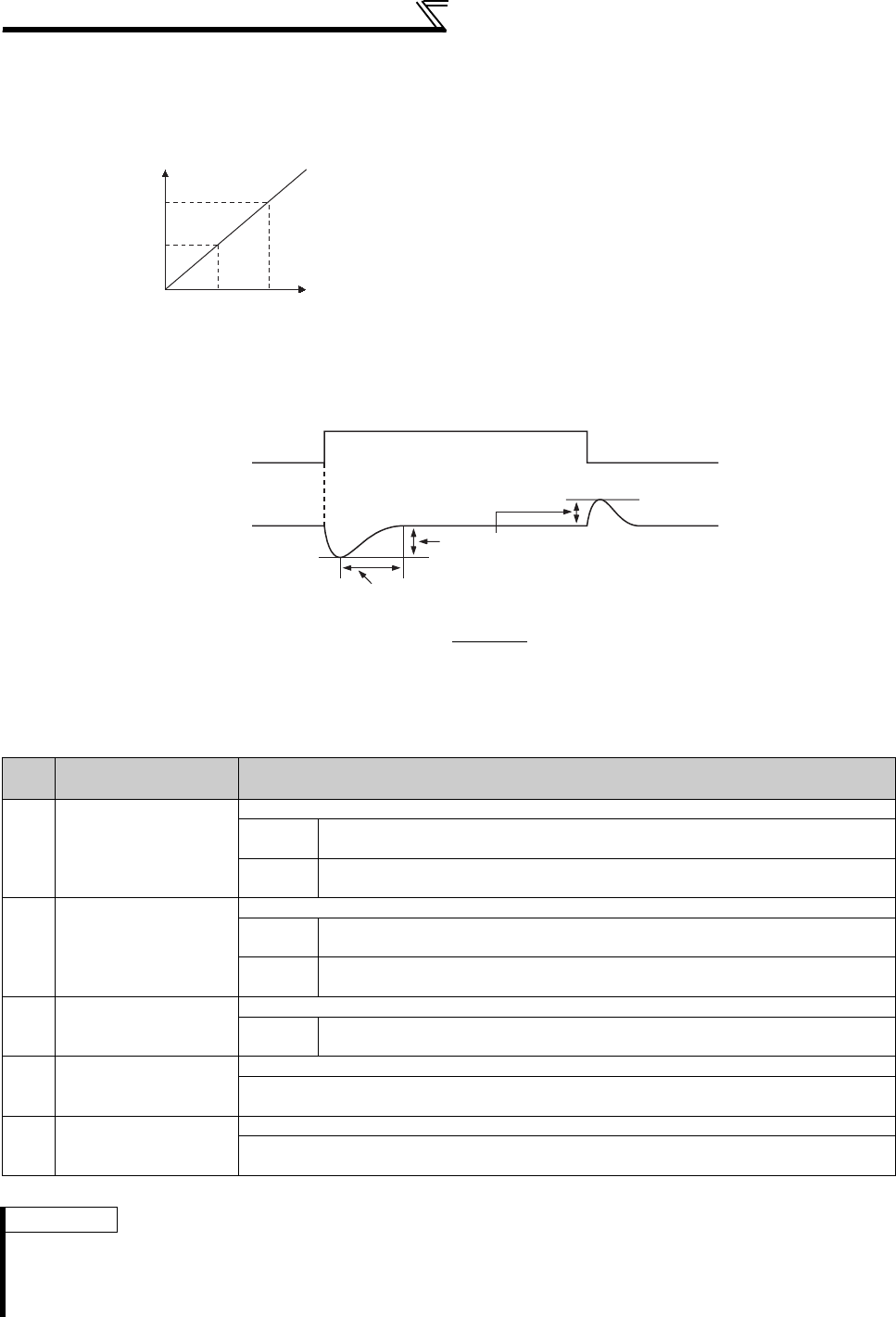
108
Speed control by Real sensorless vector
control, vector control
(5) Manual input speed control gain adjustment
· Make adjustment when any of such phenomena as unusual machine vibration/noise, low response level and
overshoot has occurred.
· When there is load inertia, the actual speed gain is as given below.
· Adjustment procedures are as below:
1)Check the conditions and simultaneously change the Pr. 820 value.
2)If you cannot make proper adjustment, change the Pr. 821 value and repeat step 1).
· Pr. 820 Speed control P gain 1 = "60%" (initial value) is equivalent to
120rad/s (speed response of the motor alone). (Half the value for
75K or higher or for Real sensorless vector control.) Increasing the
setting value improves the response level, but a too large gain will
produce vibration and/or unusual noise.
· Decreasing the Pr. 821 Speed control integral time 1 shortens the
return time taken at a speed change. However, a too short time will
generate an overshoot.
Actual speed gain = speed gain of motor without load ×
JM
JM: Inertia of the motor
JL: Motor shaft-equivalent load inertia
JM+JL
No.
Phenomenon/
Condition
Adjustment Method
1
Load inertia
is large
Set the Pr. 820 and Pr. 821 values a little higher.
Pr. 820
When a speed rise is slow, increase the value 10% by 10% until just before
vibration/noise is produced, and set about 0.8 to 0.9 of that value.
Pr. 821
If an overshoot occurs, double the value until an overshoot does not occur, and
set about 0.8 to 0.9 of that value.
2
Vibration/noise
generated from
mechanical system
Set the Pr. 820 value a little lower and the Pr. 821 value a little higher.
Pr. 820
Decrease the value 10% by 10% until just before vibration/noise is not produced,
and set about 0.8 to 0.9 of that value.
Pr. 821
If an overshoot occurs, double the value until an overshoot does not occur, and
set about 0.8 to 0.9 of that value.
3 Slow response
Set the Pr. 820 value a little higher.
Pr. 820
When a speed rise is slow, increase the value 5% by 5% until just before
vibration/noise is produced, and set about 0.8 to 0.9 of that value.
4
Long return time
(response time)
Set the Pr. 821 value a little lower.
Decrease the Pr. 821 value by half until just before an overshoot or the unstable phenomenon
does not occur, and set about 0.8 to 0.9 of that value.
5
Overshoot
or unstable
phenomenon occurs.
Set the Pr. 821 value a little higher.
Increase the Pr. 821 value double by double until just before an overshoot or the unstable
phenomenon does not occur, and set about 0.8 to 0.9 of that value.
REMARKS
· When making manual input gain adjustment, set "0" (without easy gain tuning) (initial value) in Pr. 819 Easy gain tuning
selection
.
· Pr. 830 Speed control P gain 2 and Pr. 831 Speed control integral time 2 are valid when the RT terminal is switched ON. Make
adjustments in the same way as Pr. 820 and Pr. 821.
Pr.820
Setting
100%
60%
(initial value)
Proportional gain
200 (100)rad/s*
120 (60)rad/s*
* The values for 75K or higher or for Real sensorless
vector control are indicated in parentheses.
Since increasing the proportional gain enhances the
response level and decreases the speed fluctuation.
Load
fluctuation
Speed
Decreasing the integral time shortens the return time taken.