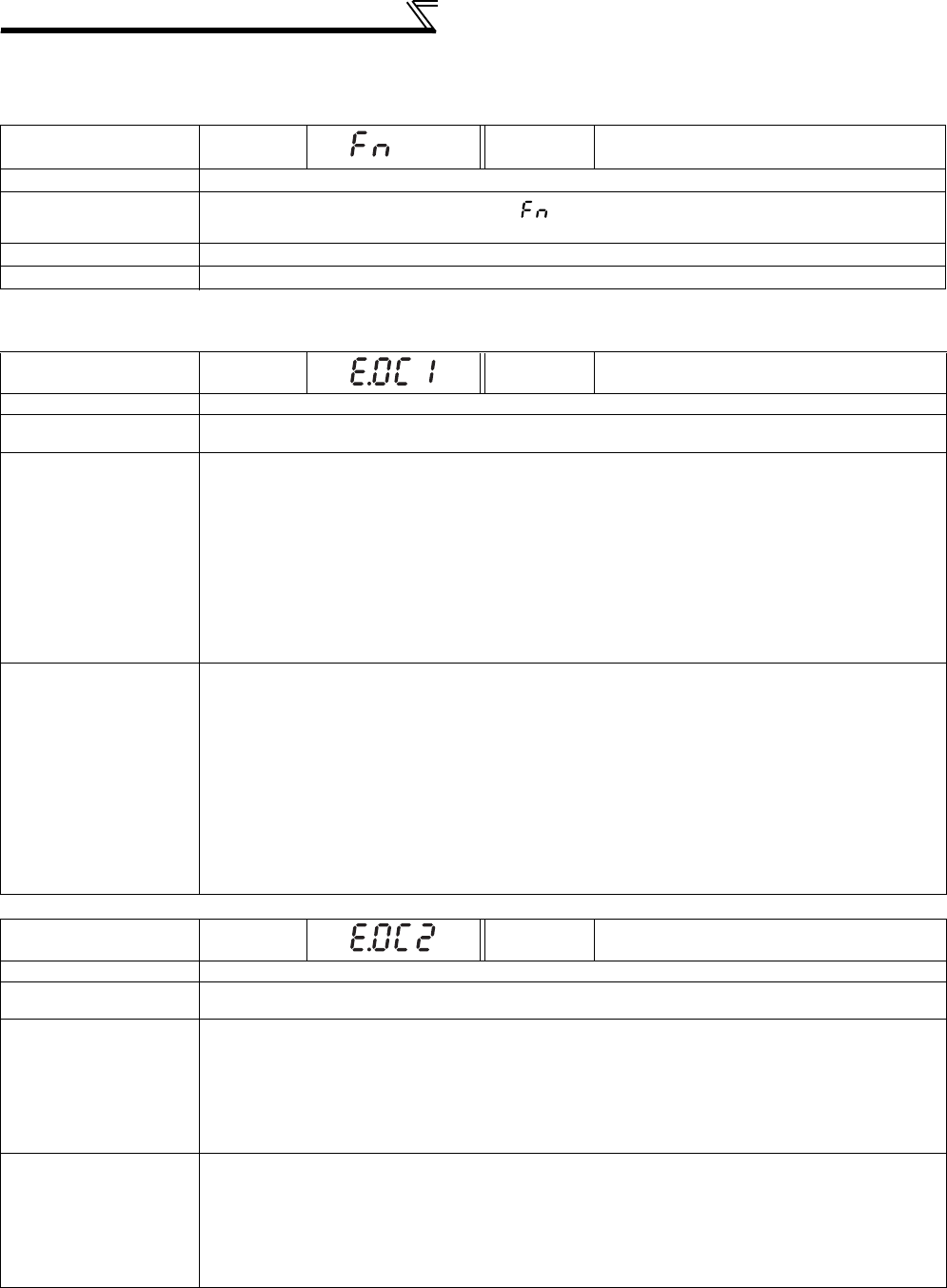
408
Causes and corrective actions
(3) Alarm
When an alarm occurs, the output is not shut off. You can also output an alarm signal by making parameter setting. (Set
"98" in any of
Pr. 190 to Pr. 196 (output terminal function selection)
.
(Refer to
page 239
.)
)
(4) Fault
When a fault occurs, the inverter trips and a fault signal is output.
Operation Panel
Indication
FN
FR-PU04
FR-PU07
FN
Name
Fan alarm
Description
For the inverter that contains a cooling fan, appears on the operation panel when the cooling fan
stops due to a fault or different operation from the setting of Pr. 244 Cooling fan operation selection.
Check point
Check the cooling fan for a fault.
Corrective action
Check for fan fault. Please contact your sales representative.
Operation Panel
Indication
E.OC1
FR-PU04
FR-PU07
OC During Acc
Name
Overcurrent trip during acceleration
Description
When the inverter output current reaches or exceeds approximately 220% of the rated current during
acceleration, the protective circuit is activated to stop the inverter output.
Check point
· Check for sudden acceleration.
· Check that the downward acceleration time is not long in vertical lift application.
· Check for output short circuit.
· Check that the Pr. 3 Base frequency setting is not 60Hz when the motor rated frequency is 50Hz.
· Check if the stall prevention operation level is set too high.
· Check if the fast-response current limit operation is disabled.
· Check that the regeneration is not performed frequently. (Check that the output voltage becomes larger
than the V/F reference voltage at regeneration and overcurrent occurs due to the high voltage.)
· Check that the power supply for RS-485 terminal is not shorted. (under vector control)
· Check that the rotation direction is not switched from forward to reverse rotation (or from reverse to
forward) during torque control under Real sensorless vector control.
Corrective action
· Increase the acceleration time.
(Shorten the downward acceleration time in vertical lift application.)
· When "E.OC1" is always lit at starting, disconnect the motor once and start the inverter.
If "E.OC1" is still lit, contact your sales representative.
· Check the wiring to make sure that output short circuit does not occur.
·Set the Pr. 3 Base frequency to 50Hz. (Refer to page 159.)
·
Lower the setting of stall prevention operation level.
· Activate the fast-response current limit operation.(Refer to page 152.)
· Set base voltage (rated voltage of the motor, etc.) in Pr. 19 Base frequency voltage. (Refer to page 159.)
· Check RS-485 terminal connection. (under vector control)
· Prevent the motor from switching the rotation direction from forward to reverse (or from reverse to
forward) during torque control under Real sensorless vector control.
Operation Panel
Indication
E.OC2
FR-PU04
FR-PU07
Stedy Spd OC
Name
Overcurrent trip during constant speed
Description
When the inverter output current reaches or exceeds approximately 220% of the rated current during
constant speed operation, the protective circuit is activated to stop the inverter output.
Check point
· Check for sudden load change.
· Check for output short circuit.
· Check if the stall prevention operation level is set too high.
· Check if the fast-response current limit operation is disabled.
· Check that the power supply for RS-485 terminal is not shorted. (under vector control)
· Check that the rotation direction is not switched from forward to reverse rotation (or from reverse to
forward) during torque control under Real sensorless vector control.
Corrective action
· Keep load stable.
· Check the wiring to make sure that output short circuit does not occur.
·
Lower the setting of stall prevention operation level.
· Activate the fast-response current limit operation.(Refer to page 152.)
· Check RS-485 terminal connection. (under vector control)
· Prevent the motor from switching the rotation direction from forward to reverse (or from reverse to
forward) during torque control under Real sensorless vector control.