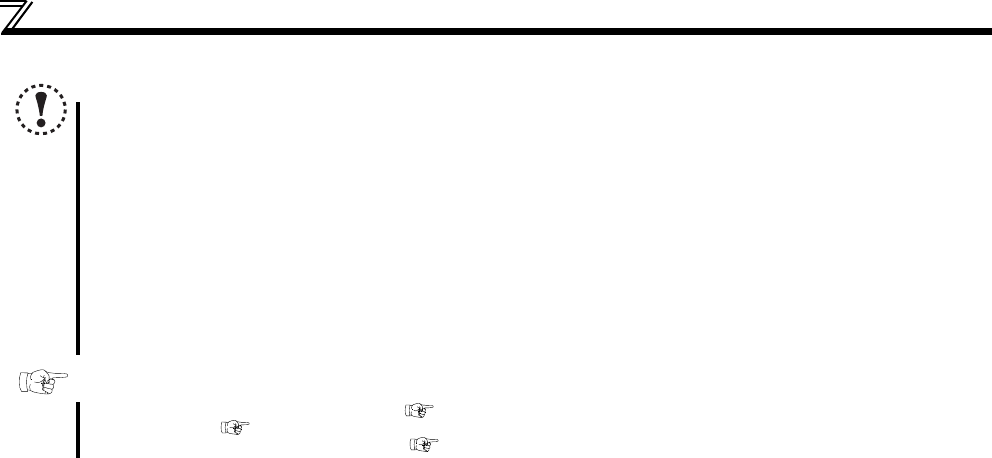
74
Adjust the output torque (current) of the motor
NOTE
The amount of current flows in the motor may become large according to the conditions such as the motor
characteristics, load, acceleration/deceleration time, wiring length, etc., resulting in an overcurrent trip (OL (overcurrent
alarm) then E.OC1 (overcurrent trip during acceleration), overload trip (E.THM (motor overload trip), or E.THT (inverter
overload trip).
(When a fault occurs, release the start command, and decrease the Pr. 0 setting 1% by 1% to reset.) (Refer to page 248.)
The Pr. 0, Pr. 46 settings are valid only when V/F control is selected.
When using the inverter dedicated motor (constant torque motor) with the FR-D720-238 and 318, FR-D740-120 and 160, set torque
boost value to 2%.
When
Pr. 0
= "3%"(initial value), if
Pr. 71
value is changed to the setting for use with a constant-torque motor, the
Pr. 0
setting
changes to 2%.
Changing the terminal assignment using Pr. 178 to Pr. 182 (input terminal function selection) may affect the other
functions. Make setting after confirming the function of each terminal.
Parameters referred to
Pr. 3 Base frequency, Pr. 19 Base frequency voltage Refer to page 85
Pr. 71 Applied motor Refer to page 103
Pr. 178 to Pr. 182 (input terminal function selection) Refer to page 113