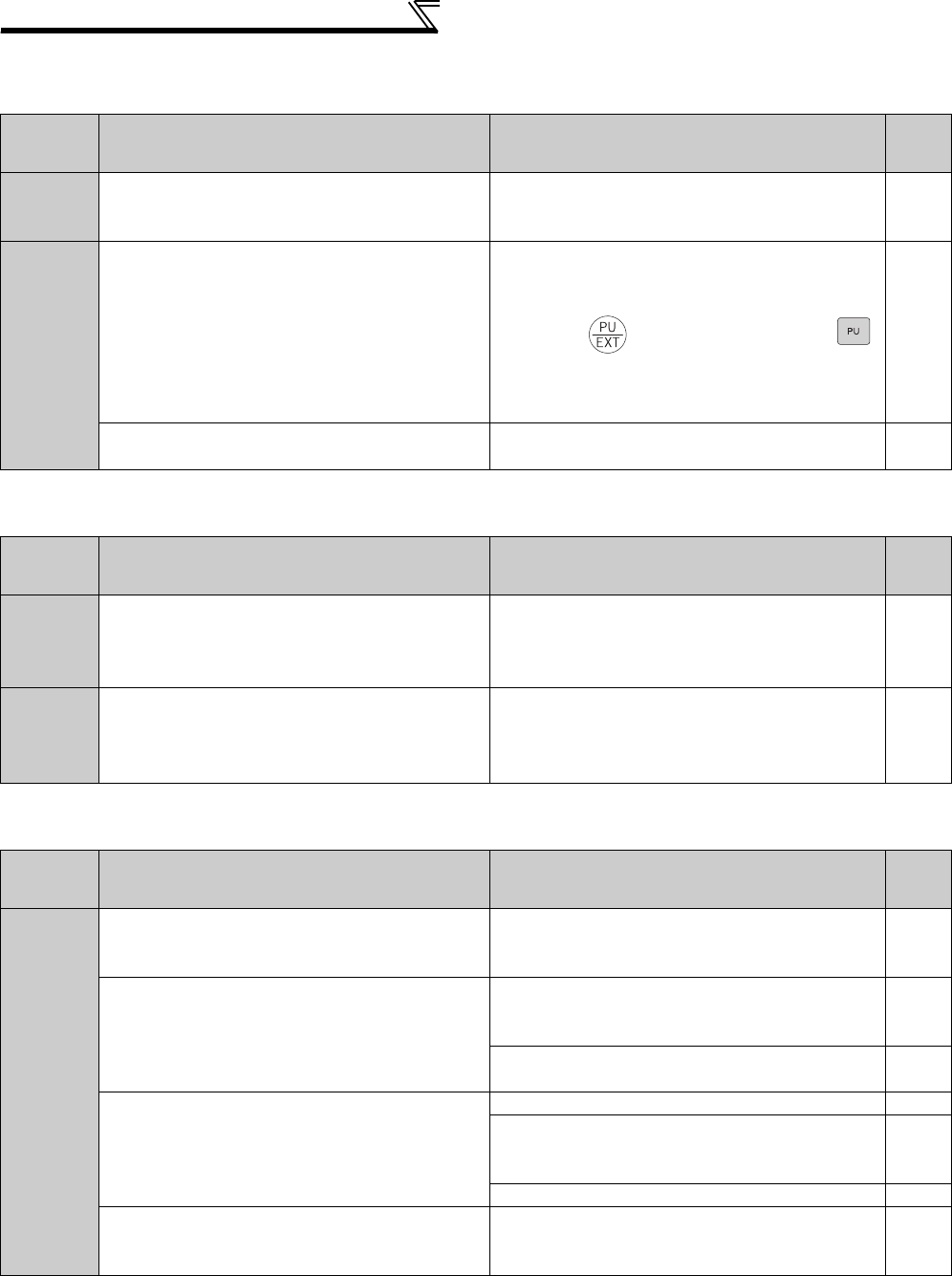
424
Check first when you have a trouble
5.5.9 Operation mode is not changed properly
5.5.10 Operation panel (FR-DU07) display is not operating
5.5.11 Motor current is too large
Check
points
Possible Cause Countermeasures
Refer
to
page
Input
signal
Start signal (STF or STR) is ON.
Check that the STF and STR signals are OFF.
When either is ON, the operation mode cannot be
changed.
313
Parameter
Setting
Pr. 79 setting is improper.
When Pr. 79 Operation mode selection setting is "0" (initial
value), the inverter is placed in the External operation
mode at input power ON. To switch to the PU operation
mode, press on the operation panel (press
when the parameter unit (FR-PU04/FR-PU07) is used) .
At other settings (1 to 4, 6, 7), the operation mode is
limited accordingly.
313
Operation mode and a writing device do not
correspond.
Check Pr. 79, Pr. 338, Pr. 339, Pr. 550, Pr. 551, and select
an operation mode suitable for the purpose.
313,
322
Check
points
Possible Cause Countermeasures
Refer
to
page
Main
Circuit,
Control
Circuit
Power is not input. Input the power. 14
Front
cover
Operation panel is not properly connected to the
inverter.
Check if the inverter front cover is installed securely.
The inverter cover may not fit properly when using wires
whose size are 1.25mm
2
or larger, or when using many wires,
and this could cause a contact fault of the operation panel.
6
Check
points
Possible Cause Countermeasures
Refer
to
page
Parameter
Setting
Torque boost (Pr. 0, Pr. 46, Pr. 112) setting is improper
under V/F control, so the stall prevention function is
activated.
Increase/decrease Pr. 0 Torque boost setting value by
0.5% increments to the setting.
146
V/F pattern is improper when V/F control is performed.
(Pr. 3, Pr. 14, Pr. 19)
Set rated frequency of the motor to Pr. 3 Base frequency.
Use Pr. 19 Base frequency voltage to set the base voltage
(e.g. rated motor voltage).
159
Change Pr. 14 Load pattern selection according to the load
characteristic.
161
Stall prevention (torque limit) function is activated due to
a heavy load.
Reduce the load weight. —
Set Pr. 22 Stall prevention operation level (Torque limit level)
higher according to the load. (Setting Pr. 22 too large
may result in frequent overcurrent trip (E.OC).)
152
(100)
Check the capacities of the inverter and the motor. —
Auto tuning is not performed under Advanced magnetic
flux vector control, Real sensorless vector control, or
vector control.
Perform offline auto tuning. 189