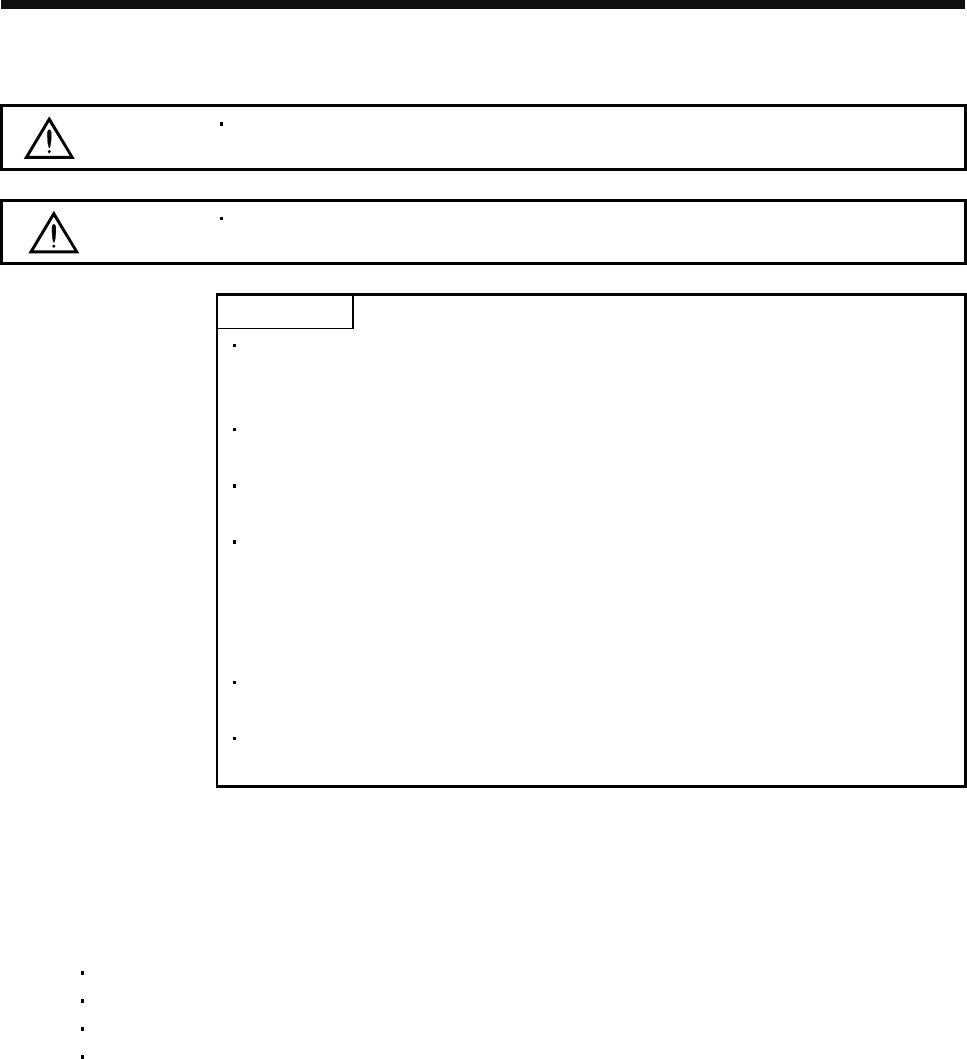
4. OPERATION AND FUNCTIONS
4 - 3
4.2.2 Driving when magnetic pole is detected
WARNING
Note that the magnetic pole detection is automatically started simultaneously with
turning on the servo-on command.
CAUTION
If the magnetic pole detection is not executed properly, the direct drive motor may
run unexpectedly.
POINT
Establish the machine configuration using the stroke limits (FLS and RLS). If the
stroke limits (FLS and RLS) do not exist, it may cause the machine damage by a
collision.
At the magnetic pole detection, it is not predictable whether it moves to the forward
rotation or reverse rotation.
Setting the parameter No.PS09 (Magnetic pole detection voltage level) may cause
the occurrence of overload, overcurrent, magnetic pole detection alarm, etc.
When performing the positioning operation from the controller, set the sequence
which confirms the normal completion of magnetic pole detection and the servo-on
status, then outputs the positioning command. If outputting the positioning
command before the Ready (RD) turns on, the command may not be accepted or
the servo alarm may occur.
After the magnetic pole detection, check the accuracy of position with the test
operation (positioning operation) of MR Configurator.
The accuracy of magnetic pole detection will be improved by being operated in the
no-load condition.
For the following cases, the magnetic pole detection is required.
(a) When using the incremental system (Refer to (1) in this section)
(b) When using the absolute position detection system and matching with the cases indicated below (Refer
to (2) in this section)
At the system setup (at the first startup of equipment)
When the direct drive motor is replaced
When the Z-phase pulse of the direct drive motor cannot be turned on manually
When the absolute position erase (25) alarm has occurred