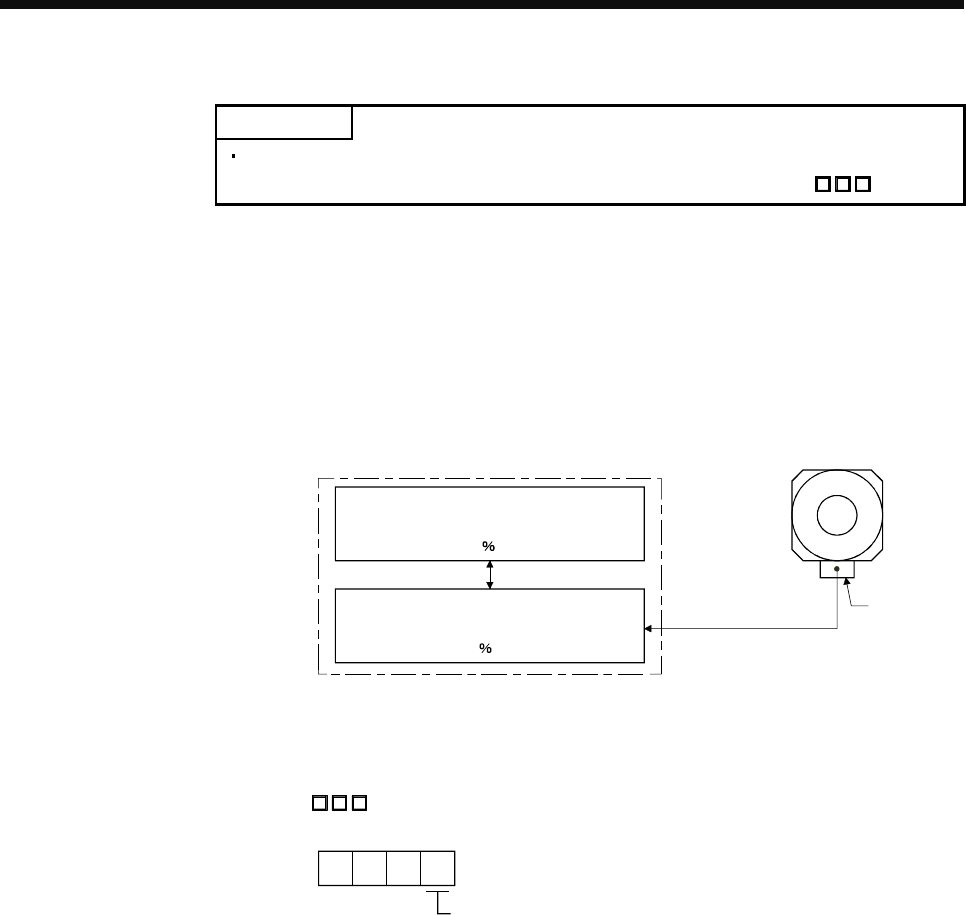
4. OPERATION AND FUNCTIONS
4 - 16
4.4 Servo control error detection function
POINT
For the servo control error detection function, the position and speed deviation
error detections are enabled as factory-set. (Parameter No.PS04:
3)
If the servo control gets unstable for some reasons, the direct drive motor may not operate properly. The
protective function for detecting this before happens and stopping the operation is the servo control error
detection function.
As the servo control error detection function, there are three types of detection methods: position deviation,
speed deviation and torque deviation. An error is detected when each error detection function is enabled with the
setting of the parameter No.PS04 (Special function selection 2). The detection level can be changed with the
parameter Nos. PS05, PS06 and PS07.
Direct drive motor
Encoder
Servo amplifier internal value
1) Model feedback position [rev]
3) Model feedback rotation speed [r/min]
5) Command torque [ ]
Encoder
2) Feedback position [rev]
4) Feedback rotation speed [r/min]
6) Feedback torque [ ]
Servo amplifier
Figure 4.1 Outline of servo control error detection function
(1) Position deviation error detection
Set the parameter No.PS04 to "
1" to make the position deviation error detection enabled.
Position deviation
error detection valid
1
Parameter No.PS04
If there is a deviation larger than the setting value (1 to 1000rev) of the parameter No.PS05 (Servo control
position deviation error detection level) after comparing the model feedback position 1) and the feedback
position 2) in Figure 4.1, the alarm (Servo control error 42) occurs, and the direct drive motor stops. The
initial value of parameter No.PS05 is 0.09rev (About 30degree in the mechanical radian). Change the
setting value as necessary.