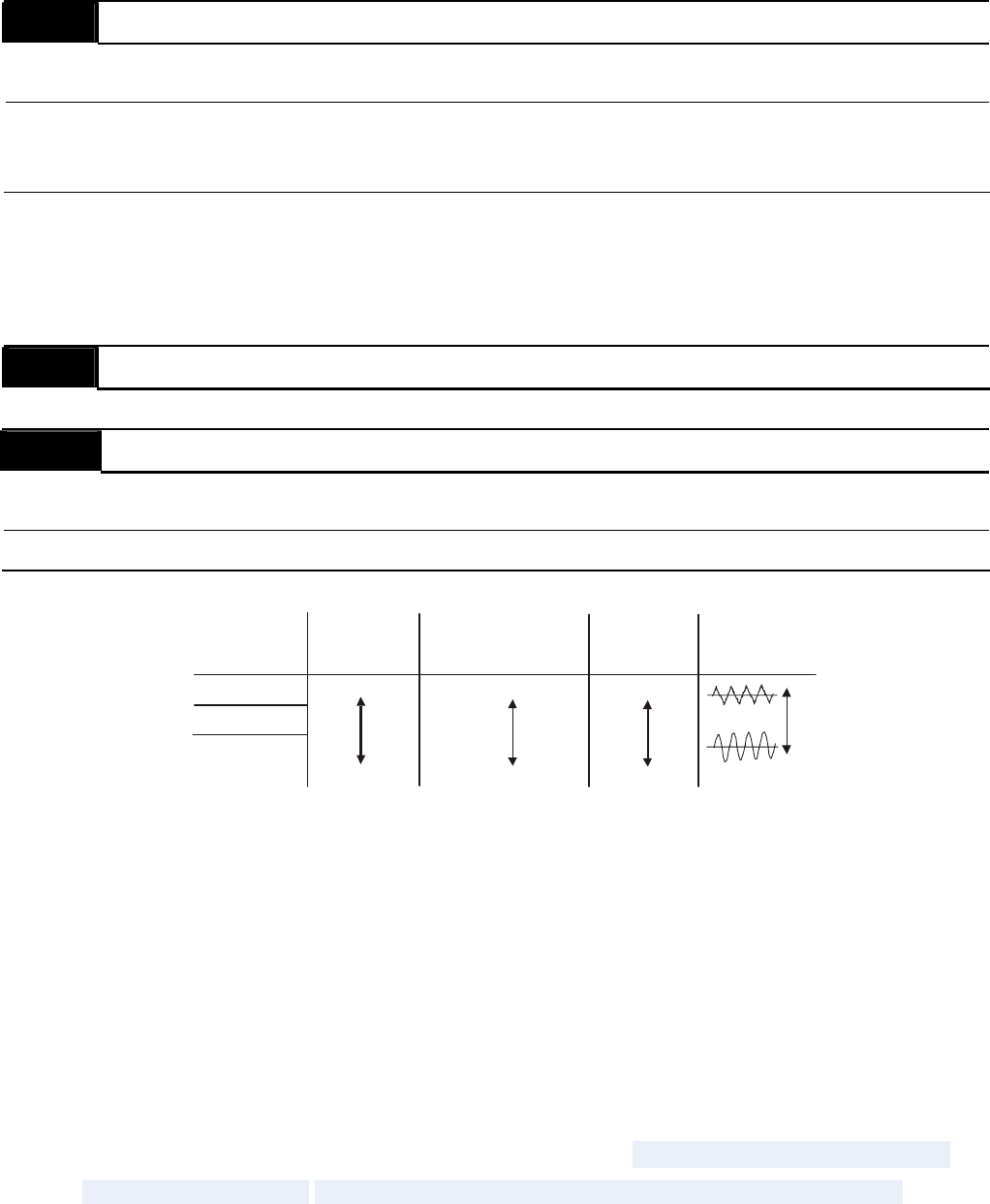
Chapter 4 ParametersAT |Troubleshooting}| BLD-E1 Series
4-38
Revision May 2009, 00DE, V0.50
This parameter determines the control method of the brushless DC motor drive:
Setting 0: user can design V/f ratio by requirement and control multiple motors simultaneously.
Setting 1: User can use PG card with Encoder to do close-loop speed control.
Setting 8: To increase torque and control speed precisely. (1:1000). This setting is only for
using with permanent magnet motor and others are for induction motor.
00-10
Speed Unit
Control
mode
VF VFPG FOCPM
Factory Setting: 0
Settings
0 Hz
3 RPM
When parameter 00.10=3, the setting of parameter 01.00, .09~01.11, 01.23, 01.29,
02.25~02.28, 04.00~04.15, 07.05, 10.17, 10.20 and 10.21 will adjust according to the
different running speed (RPM).
00-11
Reserved
00-12
Carrier Frequency
Control
mode
VF VFPG FOCPM
Factory setting: 8
Settings 2~15KHz
This parameter determinates the PWM carrier frequency of the brushless DC motor drive.
2kHz
8kHz
15kHz
Carrier
Frequency
Acoustic
Noise
Electromagnetic
Noise or Leakage
Current
Heat
Dissipation
Current
Wave
Significant
Minimal
Minimal
Minimal
Significant
Significant
From the table, we see that the PWM carrier frequency has a significant influence on the
electromagnetic noise, brushless DC motor drive heat dissipation, and motor acoustic noise.
If the ambient noise is greater than motor acoustic noise, lower PWM carrier frequency would
allow better heat dissipation.
Though a higher PWM carrier frequency will provide quiet operation, it is necessary to check
if the wiring system and anti-interference function support this action.
If carrier frequency is higher than default setting and must be lowered but meanwhile overload
has reaches the adjusting limit, then the carrier frequency (Fc) will self-adjust in response to
the ambient temperature and current level.
For example, a 460V series under ambient temperature 40 ℃, carrier frequency 15kHz and
rated output current 55% ; if rated output current is now 87%, in responding to the ambient