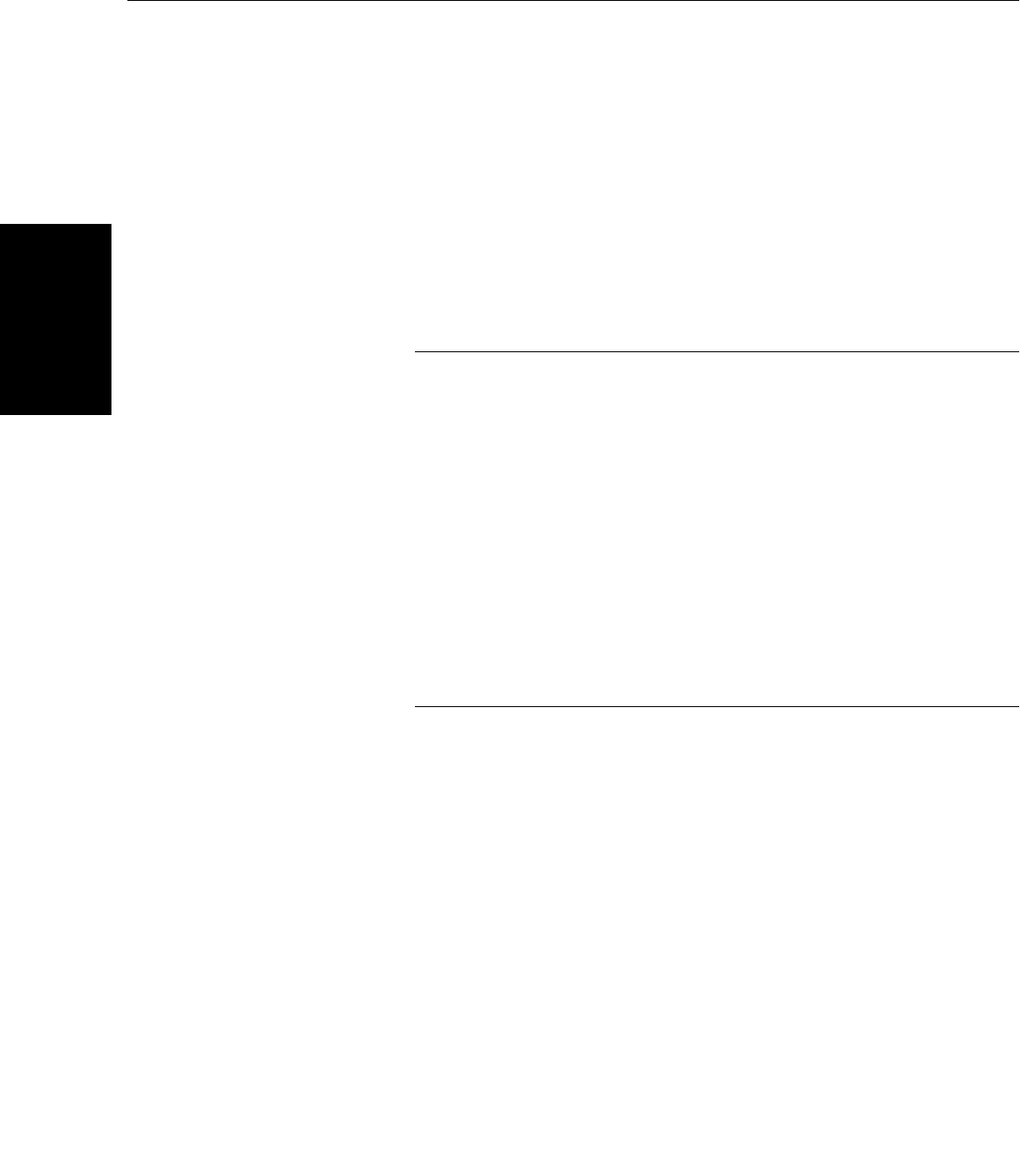
Reference Manual
00809-0100-4021, Rev DA
November 2004
Rosemount 3144P
4-22
FOUNDATION Fieldbus
Statistical Process
Monitoring (SPM)
Statistical Process Monitoring algorithm is intended to provide basic
information regarding the behavior of process measurements such as PID
control block and actual valve position. The algorithm can monitor up to four
user selected variables. All variables must reside in a scheduled function
block which is contained in the device. This algorithm can perform higher
levels of diagnostics by distribution of computational power to field devices.
The two statistical parameters monitored by the Statistical Process Monitoring
are mean and standard deviation. By using the mean and standard deviation,
the process or control levels and dynamics can be monitored for change over
time. The algorithm also provides:
• Configurable limits/alarms for High variation, low dynamics, and mean
changes with respect to the learned levels
• Necessary statistical information for Regulatory Control Loop
Diagnostics, Root Cause Diagnostics, and Operations Diagnostics.
NOTE
In Fieldbus devices, a wealth of information is available to the user. Both
process measurement and control is feasible at the device level. The devices
themselves contain both the process measurements and control signals that
are necessary to not only control the process, but to determine if the process
and control is healthy. By looking at the process measurement data and
control output over time, one can gain additional insight into the process.
Under some load conditions and process demands, changes could be
interpreted as degradation of instruments, valves or major components such
as pumps, compressors, heat exchangers, etc.... This degradation may also
indicate that the loop control scheme needs to be re-tuned or re-evaluated. By
learning a healthy process and continually comparing current information to
the known healthy information, problems due to degradation and eventual
failure can be avoided and remedied ahead of time. These diagnostics are to
aid in the engineering and maintenance of the devices. False alarms and
missed detections may occur. If a reoccurring problem in your process exists,
please contact Rosemount for assistance with the diagnostics.
Configuration Phase
The configuration phase is an inactive state when the SPM algorithm can be
configured. In this phase, the block tags, block type, parameter, limits for high
variation, low dynamics, and mean change detection can be set by the user.
The “Statistical Process Monitoring Activation” parameter must be set to
“disabled” to configure any SPM parameter. SPM can monitor any linkable
input or output parameter of a scheduled function block that resides in the
device.
Learning Phase
In the learning phase of Statistical Process Monitoring, the algorithm
establishes a baseline of the mean and dynamics of a Statistical Process
Monitoring variable. The baseline data is compared to current data for
calculating any changes in mean or dynamics of the Statistical Process
Monitoring variables.